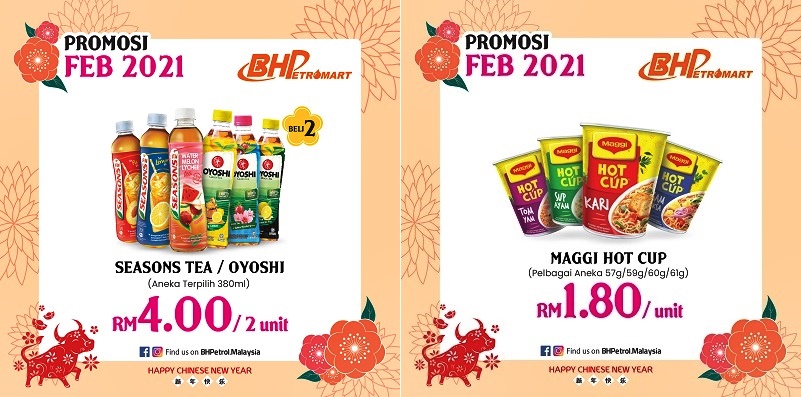
Sportscar makers – as well as every other carmaker – know that the future is electric and they cannot waste any more time just doing R&D but actually get products out on the roads for sale. Nevertheless, the process of R&D still has to continue to advance technologies as well as develop new ones.
Motorsports offer a good testbed for R&D as extreme conditions are encountered, for which solutions to problems have to be found quickly with the competitive environment. The learnings gained by the engineers can be brought back and use for production cars.
Lotus appears to be doing just that with the E-R9, a dramatic new design study for a next-generation pure electric endurance racer that could be on the starting grid of circuits around the world for the 2030 racing season.
‘E-R’ stands for Endurance Racer, while ‘9’ is the car’s competition number carefully chosen in tribute to Lotus’ racing past. It was in a Lotus Mark IX that the race team made its debut appearance at the Le Mans 24 Hours, with company founder Colin Chapman among the drivers competing. The year was 1955, meaning the E-R9 race car concept – if raced in 2030 – would be in celebration of the Mark IX’s 75th anniversary.
Technology showcase
The E-R9 has been developed by Lotus Engineering and is intended to serve as a technology showcase of Lotus philosophy, capability and innovative spirit in the fields of advanced electrified powertrains and aerodynamics. It was developed by the engineering team that included Louis Kerr, principal platform engineer on the Lotus Evija pure electric hypercar as well as technical director, GT, Geely Group Motorsports International.
Visually, it was brought to life by the Lotus Design team, led by Russell Carr, Design Director for Lotus. Finished in striking black and gold – a clear nod to Lotus’ pioneering motorsport heritage that led to 13 Formula 1 championship titles – the EV features a sleek fighter jet-style canopy centrally mounted in a delta-wing upper body.
‘Morphing’ body panels
Chief among the car’s aero innovations are its ‘morphing’ body panels. Located across the delta-wing profile, this adaptability – where active surfaces can change their shape and attitude to the air flow either at the press of a button by the driver or automatically according to performance sensor inputs – would deliver minimum drag on the straights and maximum downforce in the corners.
Vertical control surfaces at the rear would generate aerodynamic forces to help the car change direction, without the limitations of grip at the tyre contact patch. The result is a racer that’s partly driven like a car and partly flown like a fighter jet.

Technology from Evija
The E-R9 has an advanced electric drivetrain powering each wheel independently, a system enhanced with torque-vectoring. It builds on technology already integrated on the Evija though, for the E-R9, the system would be fully adjustable by the driver on the move.
“Battery energy density and power density are developing significantly year on year. Before 2030, we’ll have mixed cell chemistry batteries that give the best of both worlds, as well as the ability to ‘hot-swap’ batteries during pitstops,” predicts Kerr.
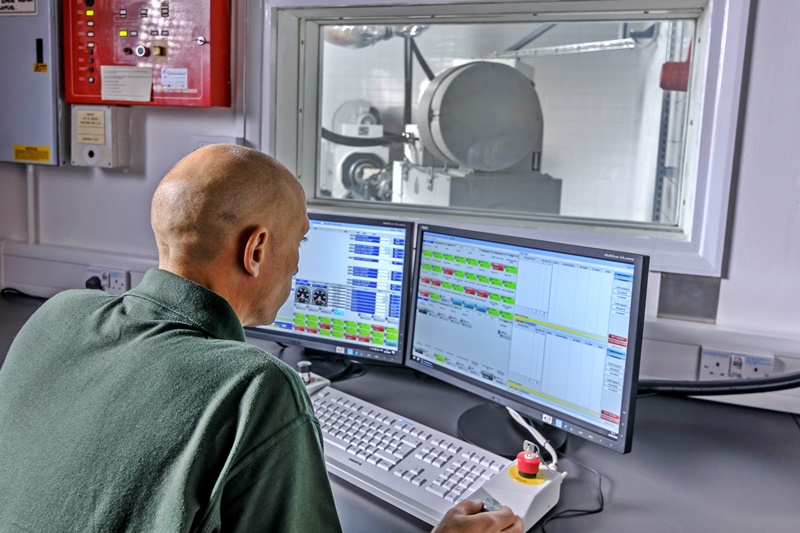
The phenomenal aerodynamics of the Lotus Evija hypercar explained