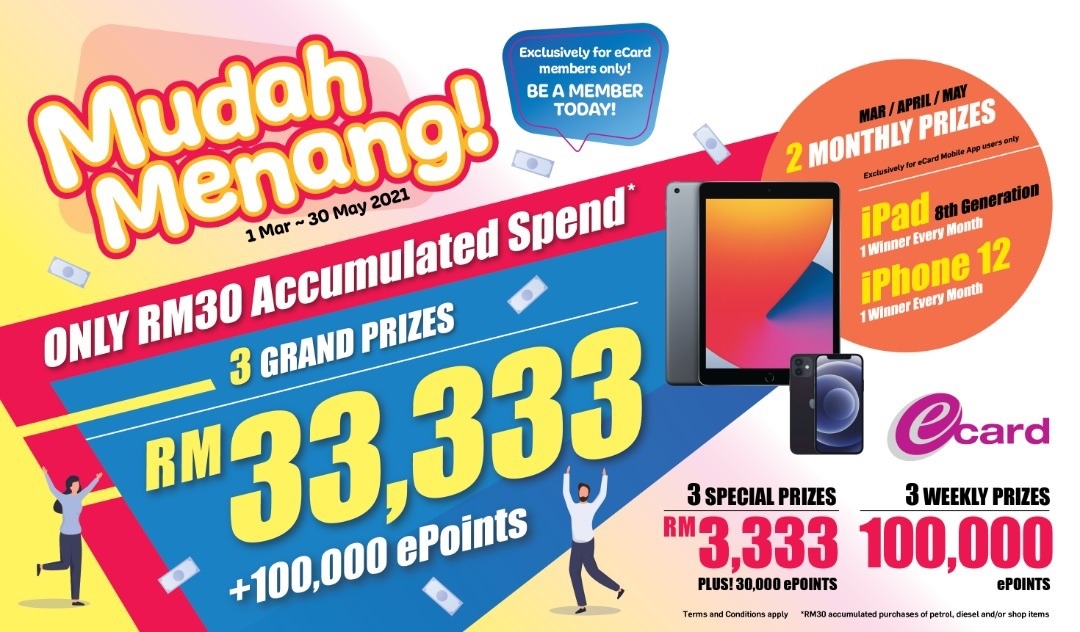
Henry Ford believed in his company owning and managing every aspect of making cars – including even owning the plantations of rubber trees that provided rubber for his cars. But as the years went by, specialisation began and while carmakers focussed on designing and manufacturing cars, some activities were also farmed out to other companies. Design, for instance, was sometimes done by external consultants more specialised in the work, notable Italian studios like Pininfarina, Ghia and ItalDesign being among them.
In the 21st century, as the whole idea of making cars changes with the transition to electric vehicles, there are many newcomers (especially in China) who want to get into the game. Some of these have experience in other types of manufacturing, eg batteries or mobilephones, but no experience in engineering cars. For them to gain that experience as the global players did will take too long; today’s companies do not have the luxury of time to learn themselves as the market is so competitive.
So the answer has been to commission companies that specialise in certain areas. In fact, Chinese companies have been doing this, not just for design but also for powertrains. There are top-notch engineering consultancies in Europe like Lotus Engineering that can develop a car on par with any experienced manufacturer – and even the established ones sometimes ask Lotus to help.
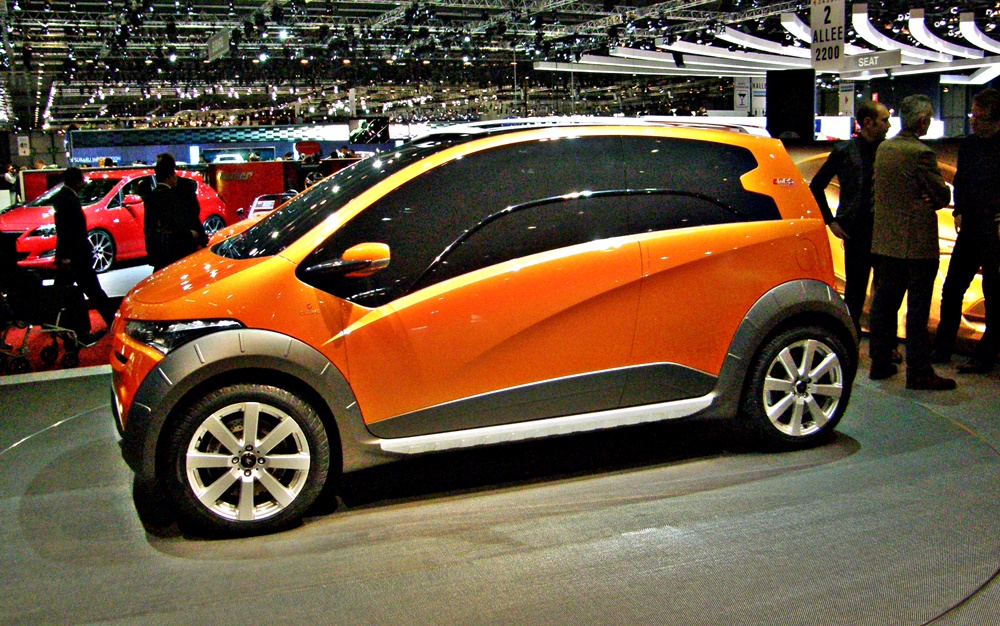
So there’s a growing business in offering a full range of services to develop cars and Italdesign has formed a partnership with Williams Advanced Engineering (WAE) to provide such services to those who want to produce and sell high-performance EVs. WAE is the technology and engineering business that was established by Williams F1. It takes technology originally developed for Formula One cars and adapts it for commercial applications.
Combining a state-of-the-art composite electric vehicle rolling chassis from WAE with turn-key vehicle development services from Italdesign, the joint venture will enable both newcomers and customers to benefit from the expertise of two global leaders in EV engineering and vehicle design, supporting them in the creation of a range of upper premium EVs from high performance GTs, crossover and sedans.
The foundation of this new venture is WAE’s innovative EV architecture – a new rolling chassis which distils WAE’s expertise in electrification, light-weighting, innovative chassis structures and vehicle and system integration into one advanced architecture known as ‘EVX’.
Differentiating itself from other EV platforms currently in the market, EVX integrates the battery pack casing with elements more commonly perceived as part of the body structure. Front and rear chassis structures mount to the carbonfibre composite case and crash loads can be transferred via internal reinforcements to the integral side sills.
The resulting higher profiled cross section achieves much of the torsional stiffness needed to deliver the full potential of the platform. These two design philosophies reduce reliance on the upper structure, which then gives greater design freedom for a variety of ‘top hats’.
Starting from WAE rolling chassis, Italdesign’s Engineering Team then complete the vehicle architecture adding safety systems, structures, and UX devices to constitute the modular platform that will be the base to build-up several different high-performances vehicles.
The innovative modular platform is ready for customisation by the Italdesign styling team who will shape the final vehicle to match the brand’s requirements in terms of marketing positioning, design direction etc. As well as being a structural component of EVX, the platform can accommodate wheelbases from 2900 mm to 3100 mm, with customers able to choose rear-wheel drive and 4-wheel drive layouts.
Combining recycled composite materials with aluminium, EVX is lightweight and sets new standards for static and torsional stiffness. With class-leading performance and mass targets, EVX will provide the perfect basis for tomorrow’s electric vehicles, supporting a flexible range of powertrain options with outstanding aerodynamics and safety performance.
Majoring on high performance, reduced time to market, flexibility and affordability at low-to-medium volumes, the new platform is capable of supporting production runs up to 10,000 units, up to 500 of which could be manufactured by Italdesign at its facilities in Italy.
WAE was the original supplier of batteries to all participants of the FIA Formula E World Championship cars in 2014, a relationship that has been revived for the 2022-23 season. WAE also supplies battery systems to ETCR and Extreme-E and has considerable experience in high-performance electrified road car programmes stretching back more than a decade.
“We are delighted to join forces with Italdesign on this exciting and timely joint collaboration” said Paul McNamara, Technical Director at WAE. “Demand for high performance electric vehicles is continuing to show considerable growth but to date, there has not been a complete EV production solution. This unique relationship brings together state-of-the-art EV rolling chassis technology with one of the world’s leaders in vehicle body engineering.”
Production-ready Nissan GT-R50 by ItalDesign makes debut on track