In a gesture that blends heritage with high-performance innovation, Lotus has unveiled the limited-run Emira Clark Edition, a tribute to the legendary Jim Clark. Developed in collaboration with the Jim Clark Trust, this special model is restricted to just 60 units and will make its global premiere as the lead car at the Formula 1 Miami Grand Prix.
The Emira Clark Edition commemorates one of motorsport’s most revered figures, whose extraordinary achievements in 1965 continue to resonate across generations. That historic year saw Clark claim the Formula 1 World Championship title with Team Lotus, while also capturing victory at the Indianapolis 500 — a feat that remains unequalled. Beyond that, Clark also dominated in Formula 2, the Tasman Series in Australia and New Zealand, and achieved success in touring car races with the Lotus Cortina.
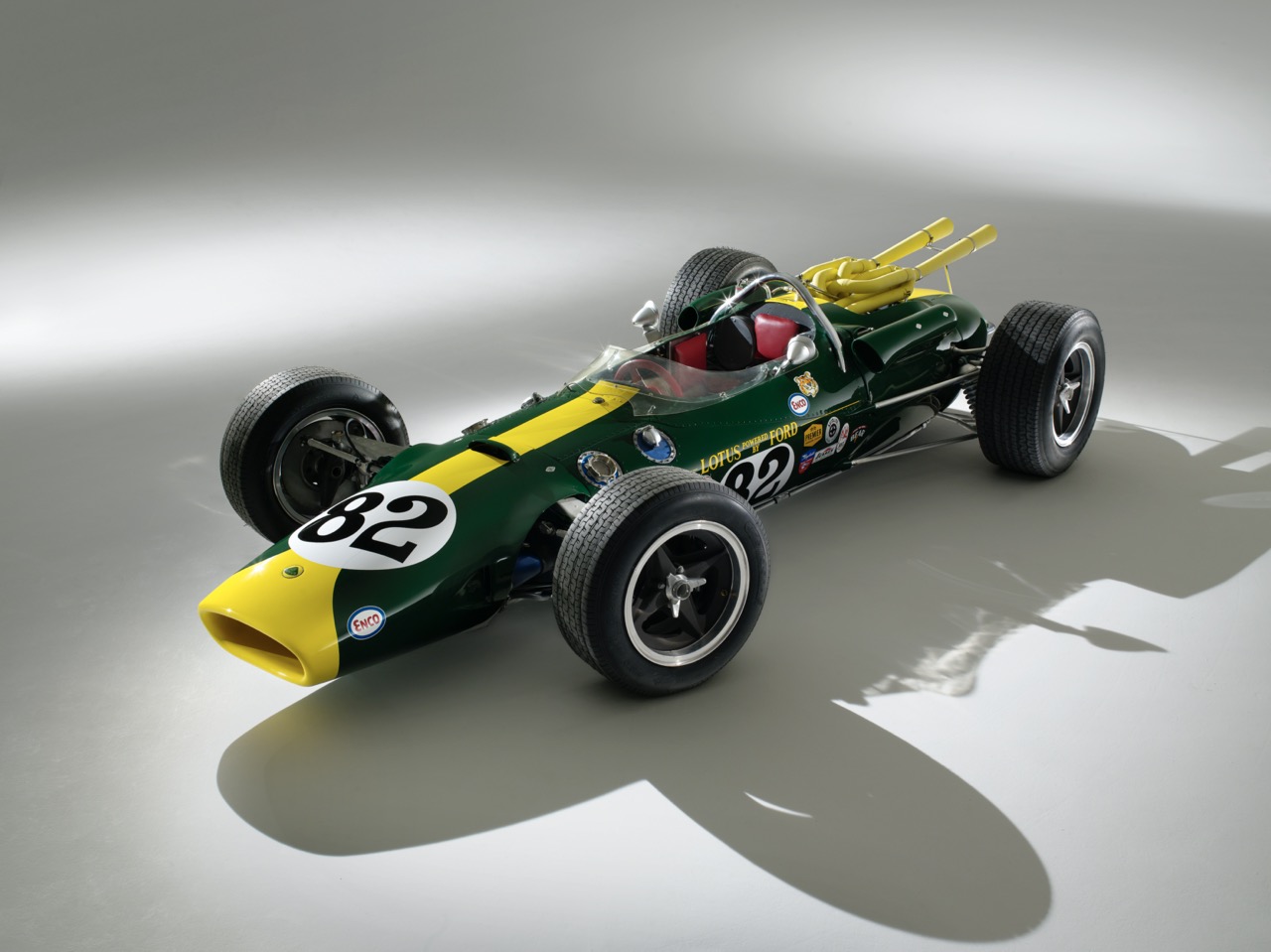
This historic campaign forms the foundation for the Emira Clark Edition’s design and ethos, celebrating Clark’s unmatched versatility and dominance across various racing formats. It stands as a modern homage to a driver whose legacy continues to influence the sport and the marque.
The car’s distinctive appearance draws direct inspiration from Clark’s 1965 Indianapolis-winning Lotus Type 38. It is painted in a bespoke Clark Racing Green finish, accented by a contrasting black roof, silver mirrors, and a striking yellow racing stripe across the nose. A machined aluminium fuel cap with a blue anodised centre, vivid yellow exhaust tips, and a hand-painted yellow pinstripe along the swage line reinforce its racing credentials. The doors are adorned with a Clark Edition emblem derived from insignia used on Clark’s original racing cars.
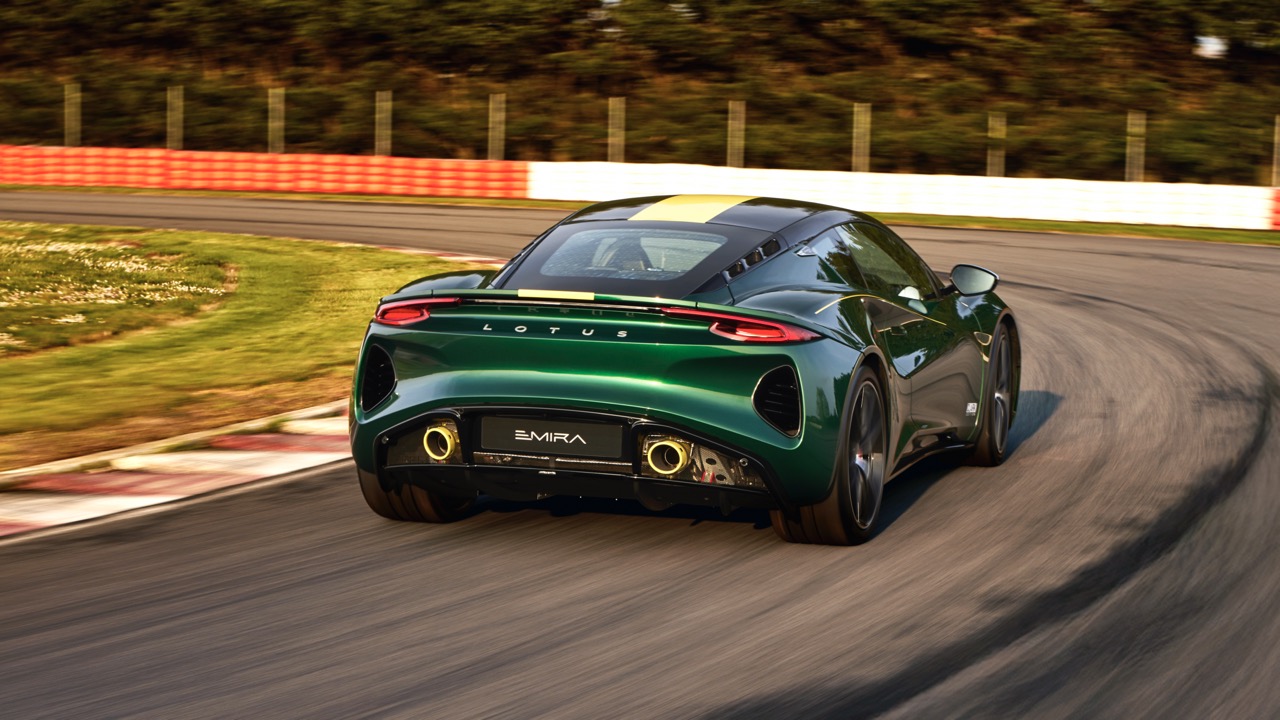
Inside, the Emira Clark Edition evokes an atmosphere steeped in motorsport nostalgia. The seats are asymmetrically upholstered — the driver’s seat wrapped in red leather and Alcantara to mirror Clark’s 1965 racing cockpit, while the passenger seat features black leather and Alcantara. A retro-style wooden gear knob enhances the period aesthetic, accompanied by commemorative Jim Clark badges which incorporate his unique family tartan from Lochcarron, Scotland. Additional design flourishes include Clark’s signature on the dashboard and Team Lotus motifs stitched into the seatbacks.
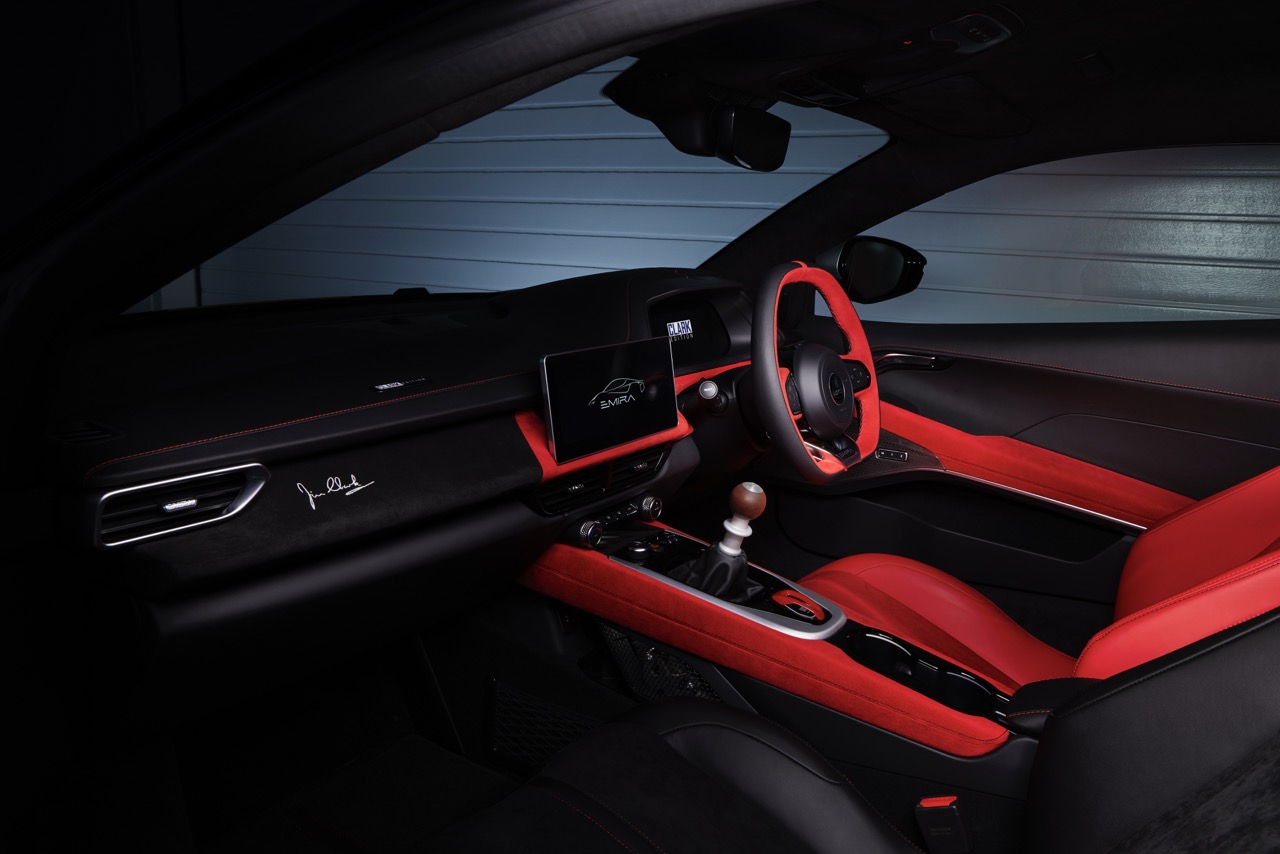
Each car will be individually numbered with carbon fibre treadplates indicating its limited production run. Buyers will also receive an exclusive hand-crafted leather holdall tailored with Clark Edition detailing, underscoring the bespoke nature of the vehicle.
Underneath its historically inspired design lies the power of the Lotus Emira V6. The special edition retains the 3.5-litre supercharged V6 engine, delivering 400hp through a six-speed manual gearbox with a limited-slip differential. Performance enhancements include unfiltered hydraulic steering, a revised exhaust note, Track Mode, and a sports suspension package courtesy of the Lotus Driver’s Pack.
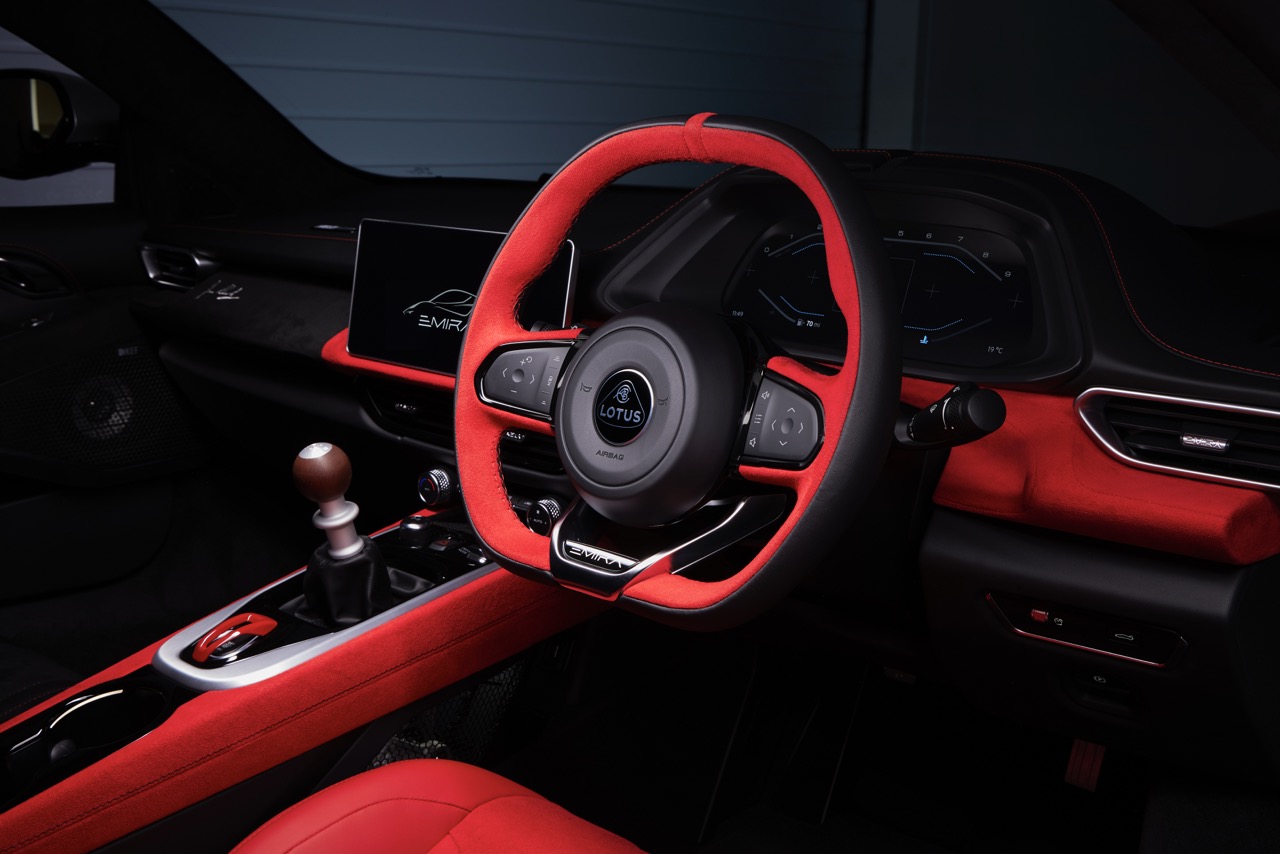
The Emira Clark Edition not only celebrates a motorsport titan but also offers a pure driving experience in keeping with Lotus’s engineering philosophy. This model stands as both a collector’s gem and a testament to Clark’s enduring influence on the world of racing.
In the United Kingdom, the Emira Clark Edition is priced at £115,000 (RM646,274), while the German market will see it listed at €140,000 (RM666,176).