For all its life, the Mini has been primarily manufactured in England. Even when the Mini became the modern MINI after the name and model rights were acquired by the BMW Group, the original factory in Oxford was also acquired to continue production of the model.
Of course, besides England, the Mini was also assembled locally in some countries, including Malaysia. Same with the MINI, which has been assembled at the Inokom plant in Kedah. Soon, the new MINI model will be produced in Germany for the first time, at the BMW Group’s plant in Leipzig. This makes the production facility the first plant at which vehicles of the BMW and MINI brands are manufactured together.
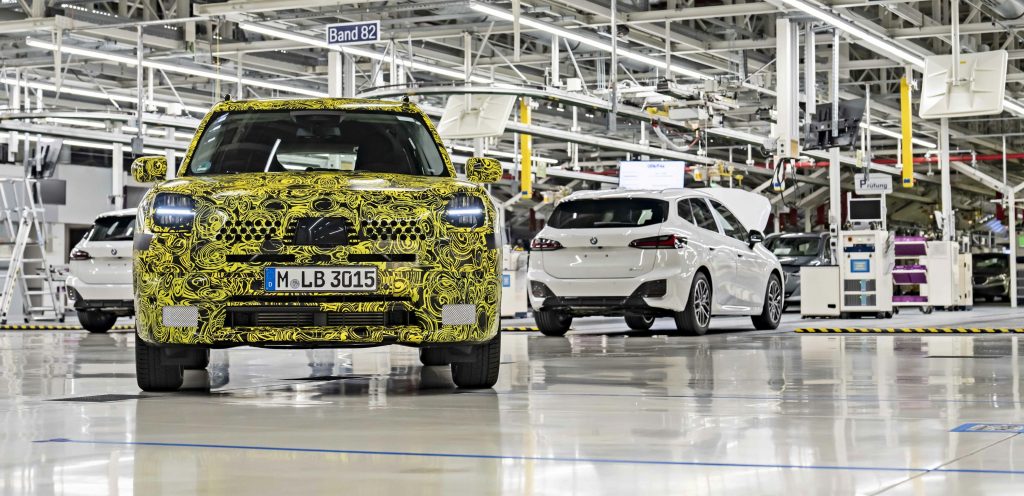
Plant Leipzig, as it is known, is the BMW Group’s sustainable production site. As the company’s pilot project for establishing a “green plant”, it is one of the most modern and sustainable automotive factories in the world. It is the first automotive plant in the world to use a newly developed burner technology in the paint shop that can use green hydrogen instead of natural gas.
As MINI’s largest model, the new all-electric Countryman will lead the new family of the brand into an era of locally emission-free electromobility. The transformation to an all-electric brand by 2030 begins with this model generation that will have a minimal ecological footprint. In combination with the use of green electricity in production, CO2 emissions can be significantly reduced compared with conventional manufacturing processes.
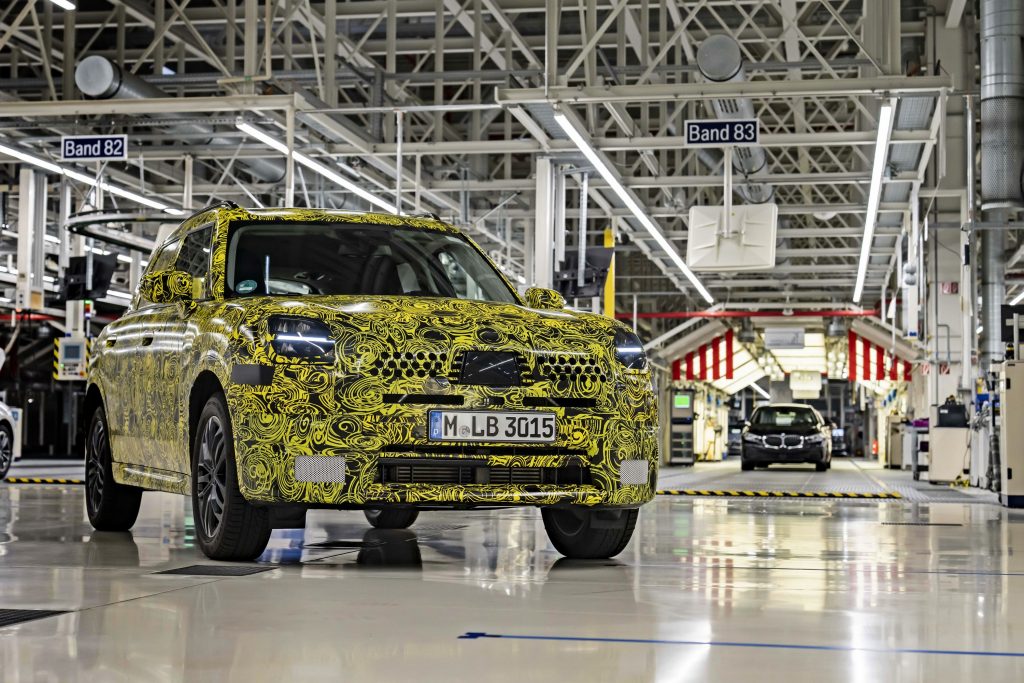
Besides being made in a green factory, the new Countryman itself also has the greatest possible environmental compatibility in production. This includes leaving out all decorative elements in the exterior and interior, and manufacturing the cast light-alloy wheels from up to 70% secondary aluminium.
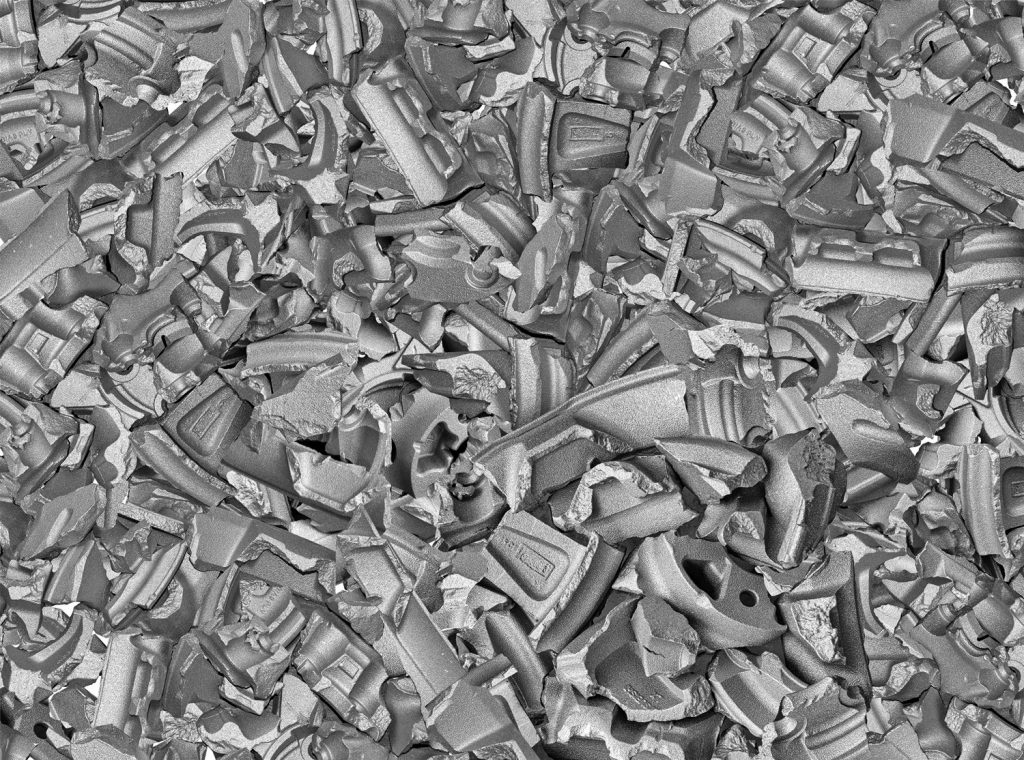
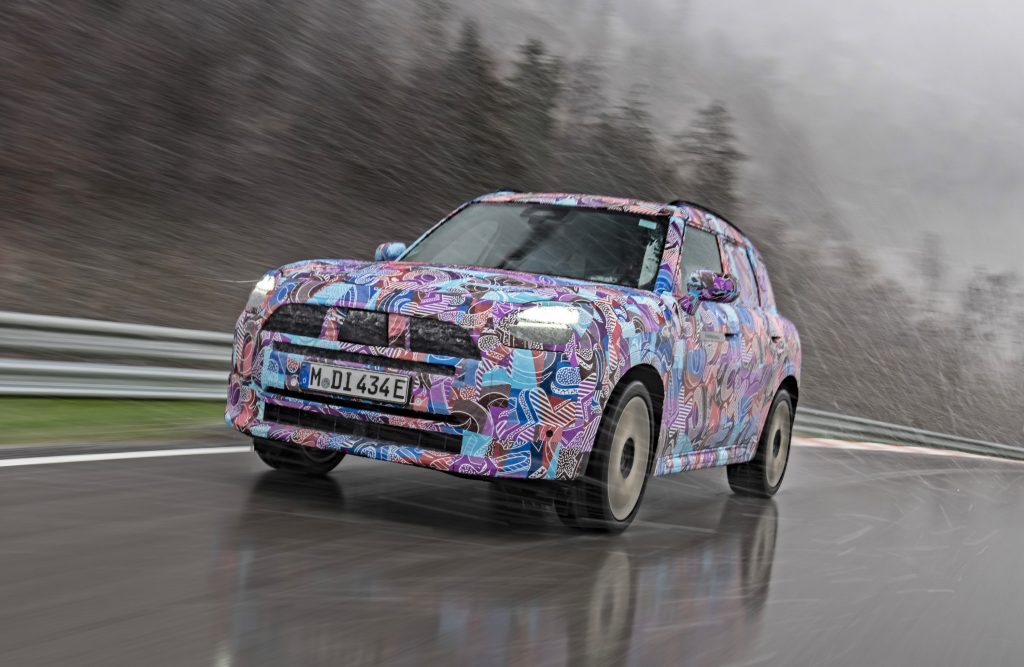
The first use of secondary aluminium for light-alloy wheels on a volume-produced model started with the current Cooper SE Convertible. The consistent use of recycled aluminium not only conserves raw material sources, but also eliminates the particularly energy-intensive electrolysis process that is normally necessary to produce light alloy.
The new generation of the Countryman E will have a power output 140 kW/191 ps, while the Countryman SE ALL4 will generate 230 kW/313 ps, including a temporary boost. The latter will be the brand’s first AWD fully electric vehicle with integrated drive units on the front and rear axles. The capacity of the lithium-ion battery pack will be 64.7 kWh, which will give an estimated range of around 450 kms.
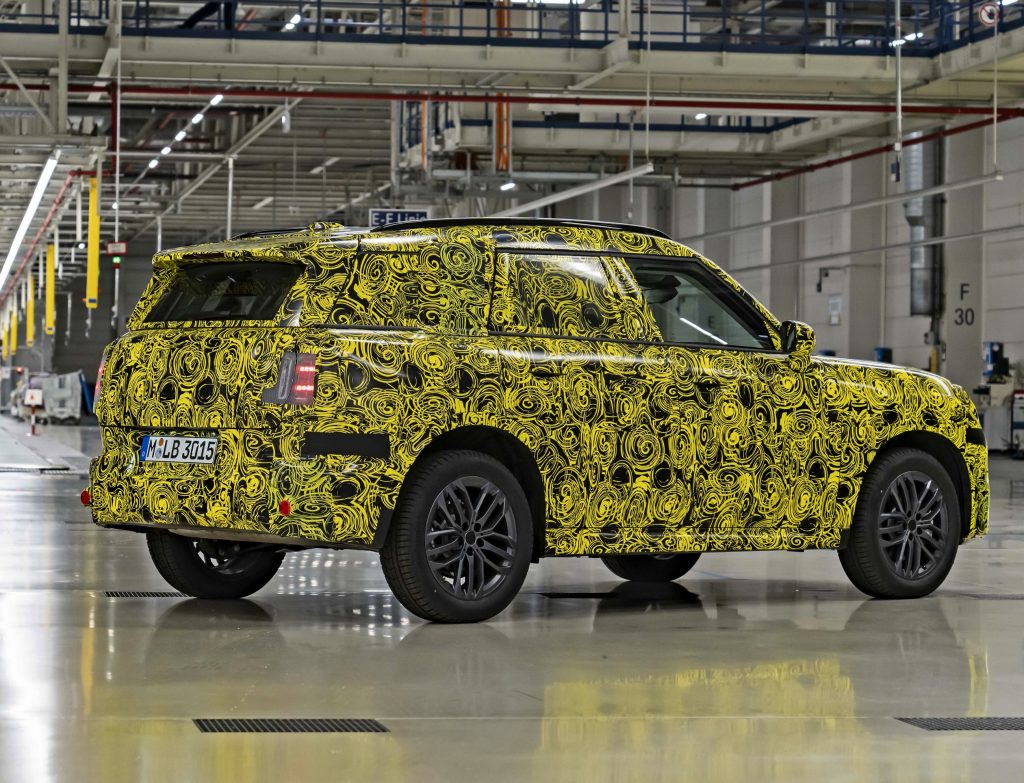
With its length increased by 13 cm to 4429 mm, the crossover will have more space which should benefit the occupants with better comfort. It is also taller by 6 cm, with the roofline at 1613 mm so there should be more headroom as well.
The surfaces of the dashboard, steering wheel, vehicle headliner and floor, and floor mats are made of recycled polyester obtained from PET bottles and carpet remnants. This high-quality, colourful and comfortable alternative to traditional materials reduces CO2 emissions along the value chain by up to 85% and emphasizes the focus on minimizing the ecological footprint.

The boom in demand for electrified MINI vehicles was apparent in 2022 with a 25.5% increase in sales compared to 2021. With 43,744 units sold worldwide last year, the all-electric Cooper SE was, by far, the most popular model in the range. Purely electric vehicles already account for 15% of total global sales.