The basic idea of an electrified powertrain is that there is one electric motor (or more) powering the wheels which receives electricity from a battery pack. Besides these two main elements, there are also ancillary systems which support their operation. In most cases, each is a separate component in the drivetrain.
Nissan has announced a new approach which it will take to electrified powertrain development, which it calls ‘X-in-1’. Under the approach, core EV and e-POWER powertrain components will be shared and modularized. This can bring about a 30% reduction (compared to 2019) in development and manufacturing costs by 2026.
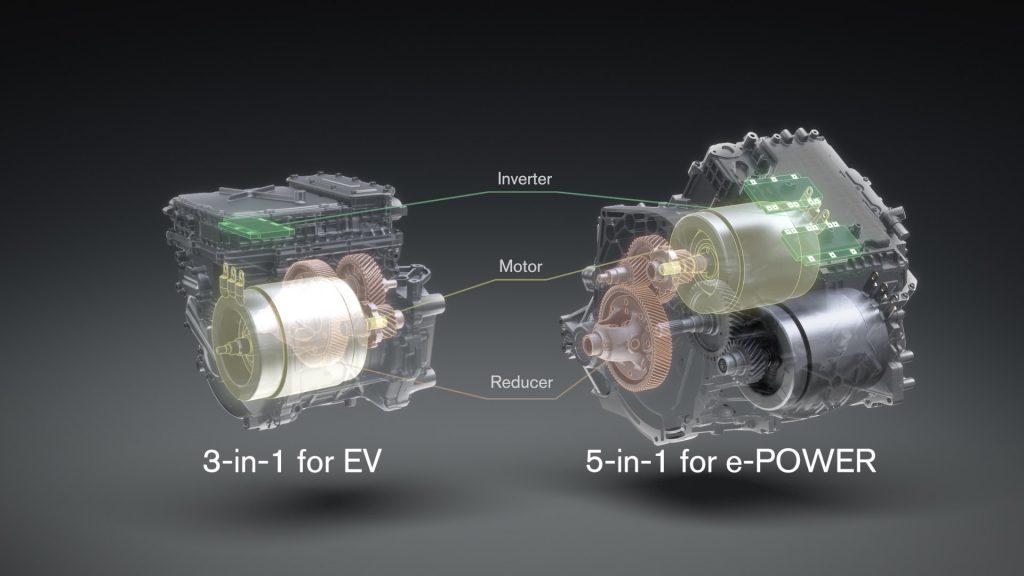
Through the X-in-1 approach, Nissan expects to be able to further increase the competitiveness of its EV and e-POWER vehicles. Under its long-term vision, Nissan Ambition 2030, the company aims to bolster its line-up with 27 new electrified models, including 19 EVs, by fiscal year 2030. The carmaker wants to bring the unique value of its electrified vehicles to the broadest range of customers by introducing the most suitable models to each market at the appropriate time.
Senior Vice President Toshihiro Hirai, who leads powertrain & EV engineering development, said: “We make the most of our expertise and know-how from our more-than-a-decade long development and production of electrified technologies. Through our innovations in electrified powertrain development, we’ll continue to create new value for customers and deliver 100% motor-driven vehicles – EVs and e-POWER – as widely as possible.”
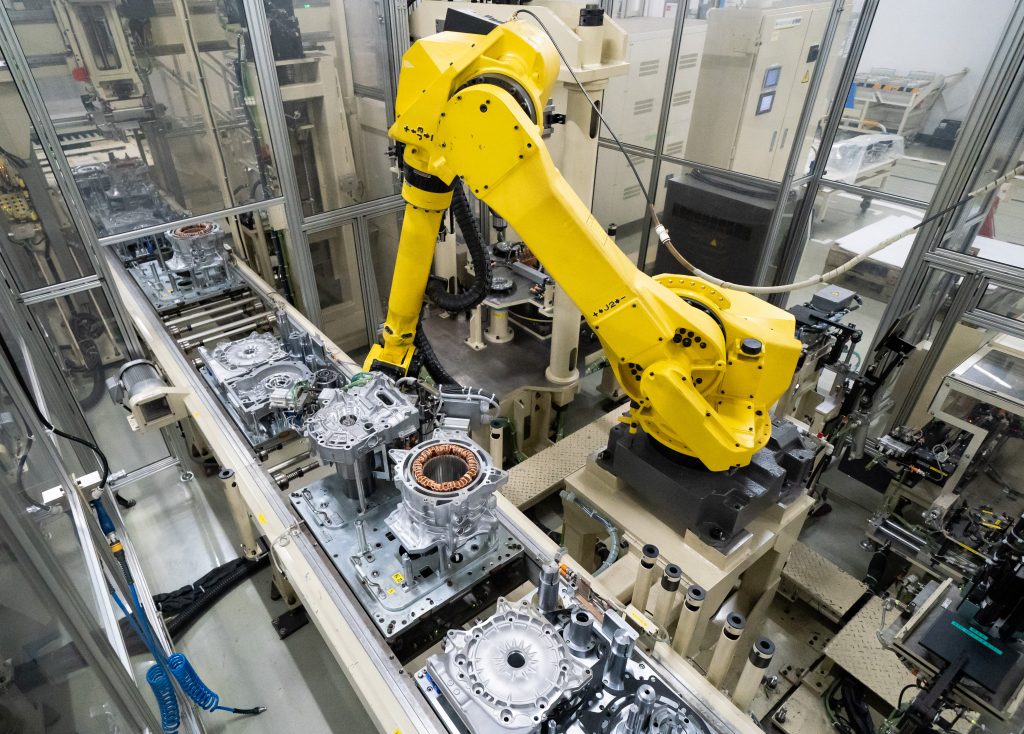
The X-in-1 approach, which covers 3-in-1, 5-in-1, and other possible variants, has been developed to enable EV and e-POWER core components to be produced on the same line. With the 3-in-1 electrified powertrain, the motor, inverter, and reducer are modularised and is planned for use in EVs. A 5-in-1 version, which additionally modularizes the generator and increaser, is planned for use in e-POWER vehicles.
With the X-in-1 approach, sharing and modularizing core components improves production efficiencies and reduces electrified powertrain costs. This can bring e-POWER price to parity with combustion engine vehicles by around 2026.
Size and weight reduction of the unit improves vehicle driving performance and minimizes noise and vibration. The adoption of a newly developed motor reduces the use of heavy rare earth elements to 1% or less of magnet weight.
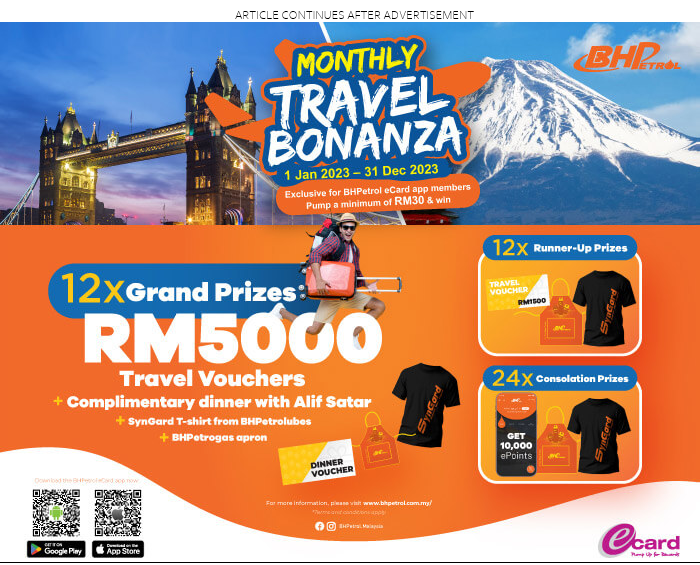
In another strategy to being about cost parity between EV and combustion engine vehicles, thereby increasing adoption of EVs, is development of battery technology. Nissan is focussing on all-solid-state batteries (ASSB) as its next-generation battery. Such batteries are more stable and safer than the lithium-ion batteries and recharge at one-third the time it takes today.
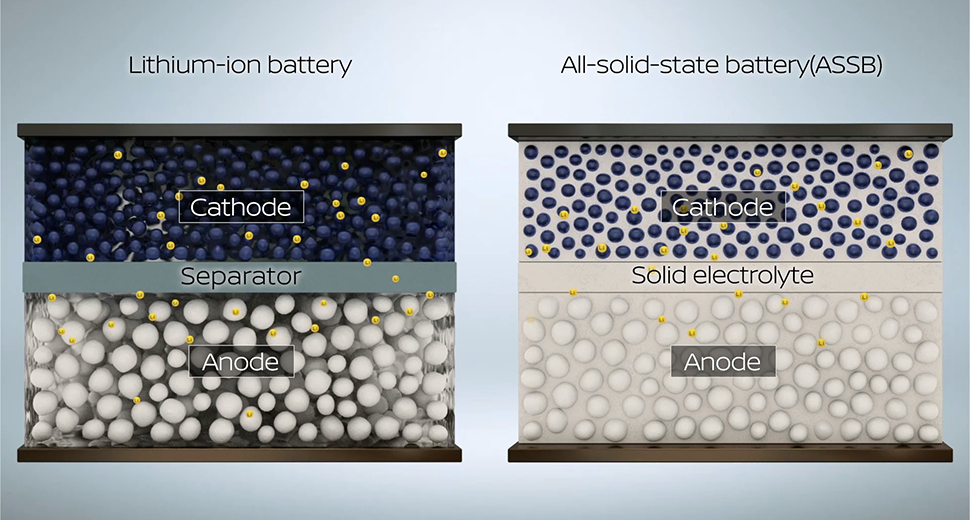
Nissan is working on lowering battery costs and will have a pilot ASSB production line by 2024 at its plant in Yokohama. The batteries will be used on a small scale until 2028 when the company expects to start marketing them widely.
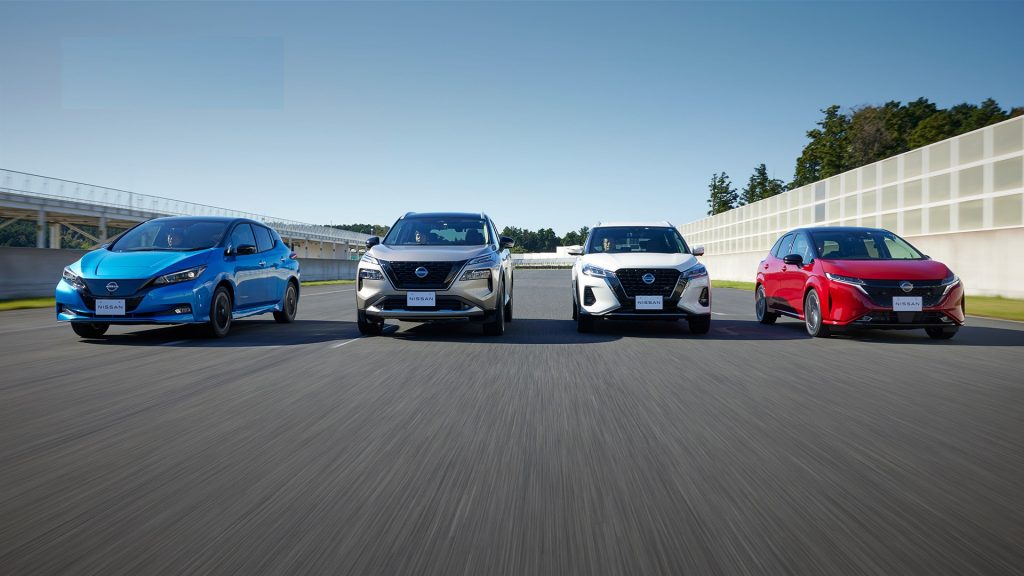