At different periods, manufacturers have different strategies which require investments in different parts of the world. In the 1990s, Ford decided that it must ‘control its own destiny’ in the ASEAN region and was attracted by the ASEAN Free Trade Area (AFTA). This would be a single trading region and those who made their products in any country in the region could export to another ASEAN country with no import duties imposed. For a mass producer like Ford (and the company was the one that introduced mass production to the auto industry), this was ideal as it meant that a mega-factory could be set up in one country to supply to other countries. Great for cost efficiencies which would also mean more competitive prices in the markets.
So Ford invested US$500 million (RM2.107 billion) to establish a brand new factory in Rayong, on the Eastern Seaboard of Thailand. The factory, called Auto Alliance Thailand (AAT), was a joint-venture with Mazda, which was then an affiliate. Its main product would be the new Ford Ranger truck and Mazda equivalent, the BT-50, with the Everest SUV being added later. Besides supplying the Asian market, the factory also supplied to other global markets which was helpful during the regional downturn when the Asian Financial Crisis hit.
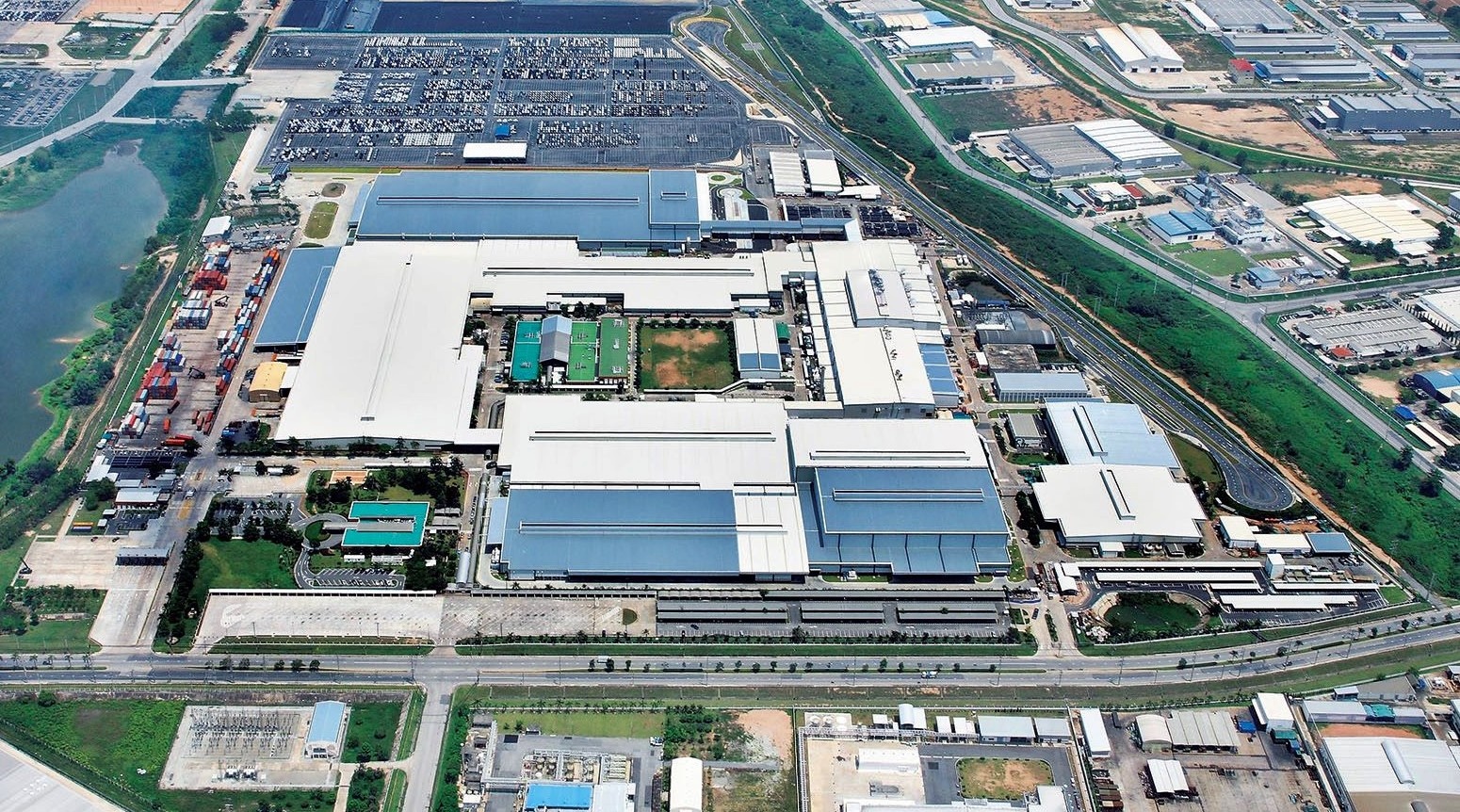
17 years after AAT began operations, Ford set up another factory in the same area with an investment of US$450 million (about RM1.9 billion) and it was wholly owned by the carmaker. Known as Ford Thailand Manufacturing (FTM), it was initially producing passenger car models like the Fiesta and Focus but when Ford decided to change strategies in the Asian region and focus on trucks, the factory switched to making only Rangers.
Ford built the second factory as demand for the Ranger grew. This was necessary as the 270,000-unit output from AAT was strictly fixed at 50:50 for each of the brands. This meant that Ford could get no more than 135,000 vehicles a year, even if Mazda did not use up its full allocation. Mazda too would have experienced the same frustration as the popularity of its models grew and one solution has been that its new BT-50 truck is now being produced at Isuzu’s factory (also in Thailand). In order to raise its output, Ford moved some production of the Ranger to FTM in 2016.
Next year will see the new generation of the Ranger entering the market and Ford expects demand to be even higher. Since its output from AAT remains capped, it is expanding FTM and is spending another US$900 million (about RM3.8 billion) on upgrading its manufacturing facilities and capabilities in Thailand, at both FTM and AAT. Over 44% of the investment is in the supply chain network to provide opportunities for local supply chain partners.
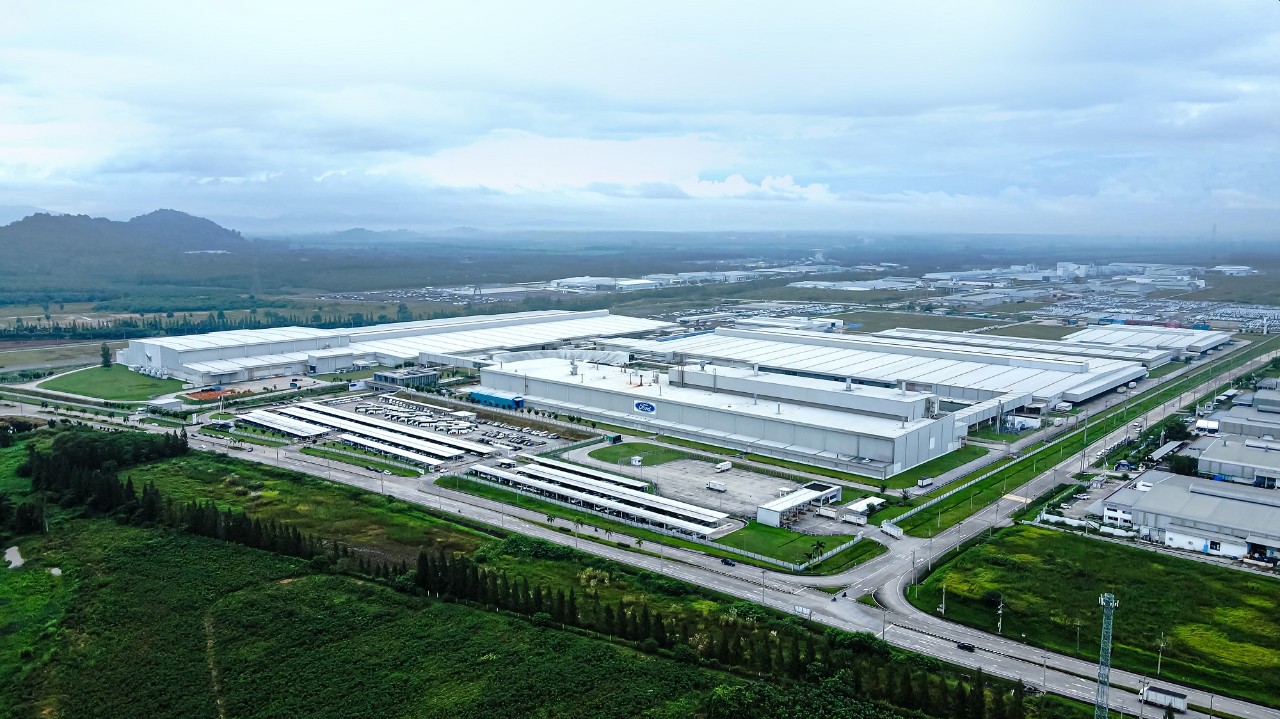
This is the largest-ever single investment in Ford’s 25-year history in Thailand and is recognition of the importance of the country as a global export production base for the company. “This is an important milestone to build on our quarter-century of commitment to producing vehicles in Thailand, enabling us to further modernize and upgrade our local operations, and support production for the exciting upcoming launch of the next-gen Ranger, one of Ford’s highest volume and most successful vehicles anywhere in the world, and the next-gen Everest SUV,” said Yukontorn ‘Vickie’ Wisadkosin, President, Ford ASEAN and Asia Pacific Distributors Markets.
Besides adding a second shift at FTM which provides over 1,200 new jobs, the overall investment also brings Ford’s manufacturing facilities in Thailand in line with the latest global efficiency, flexibility, and quality processes through extensive upgrades and new state-of-the-art manufacturing technologies.
The company is almost doubling the number of robots at both FTM and AAT, with the addition of 356 robots at the body shop and paint shop. This brings the level of automation at the body shop at FTM and AAT from 34% to 80% and 69%, respectively.
Ford also has increased its production capability for multi-variant truck production in FTM. By increasing model flexibility, the plant can produce multiple cab styles – single cab, open cab and double cab – on the same production line. This allows more flexibility in planning and scheduling so the plant can react more quickly to customer demand and reduce customer waiting time for a new vehicle.
As part of the investment, Ford is the first auto manufacturer to implement ScanBox technology in Southeast Asia. This latest surface scan capability improves the time used to accurately measure the whole vehicle by 5 times during the assembly process, helping Ford to increase efficiency in problem solving for better quality control.
In addition, FTM and AAT are making significant efforts to support environmentally friendly initiatives, including using renewable energy, reducing CO2 emissions, and practicing zero waste to landfill.
Exporting vehicles is a significant part of Ford’s manufacturing business in Thailand, with the Ranger going to over 180 markets around the world. AAT will be the lead production hub for the upcoming next-gen Everest SUV which would almost certainly be based on the new Ranger.