Porsche to assemble in Malaysia? That’s the current topic among enthusiasts following a report in The Edge Weekly. The business website mentions that its source has said the investment has been approved by Malaysian authorities and that the assembly will be done at the Inokom factory in Kedah.
It would be quite an unusual development for the German sportscar maker as it has never built its cars outside Germany. It has two factories – the original one at Zuffenhausen and the 19-year old one in Leipzig. In its 2019 financial year, total production from the two factories was almost 275,000 vehicles.
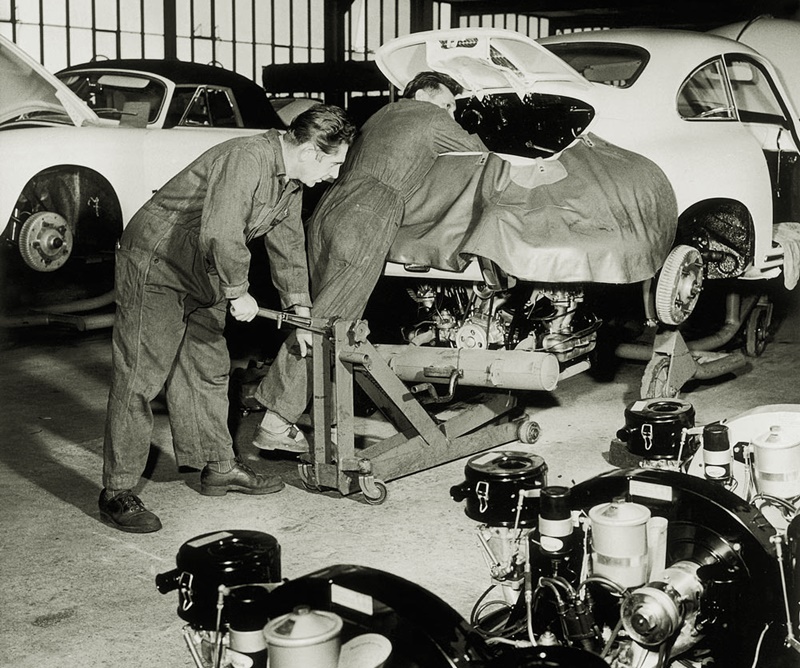
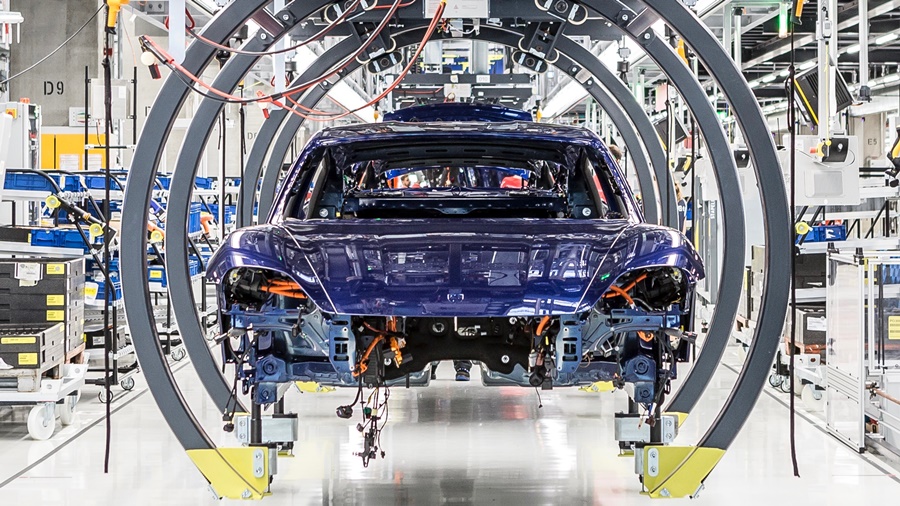
Porsche being a strong brand, demand for its products has always been good although the coronavirus pandemic which impacted the auto industry did result in a 12% decline in deliveries last year. In the first half of 2020, Porsche sold 55,550 vehicles to customers in the Asia-Pacific, Africa and the Middle East regions, with China’s intake of 39,603 units making it the biggest single market worldwide for the carmaker.
So is it time for Porsche to establish a production hub in the Asia-Pacific region? Bear in mind that the 100,000+ volume is made up of 5 model lines with the specialized all-electric Taycan being the sixth. Obviously, assembling outside Germany would not involve all the models so it would be one or two, with the Cayenne being the most popular so it could be a good candidate.
Manufacturers invest in overseas production facilities in places where they can get good incentives by government to do so. They obviously require a good infrastructure as well. At one time, the potential domestic market volume was important since they would assemble in another country and primarily want to sell there, with exports being secondary. However, with the formation of the ASEAN Free Trade Area (AFTA) as a single trading bloc and duty-free exchange of goods, it is no longer just one country to look at but the potential of regional volume, which can be quite big.
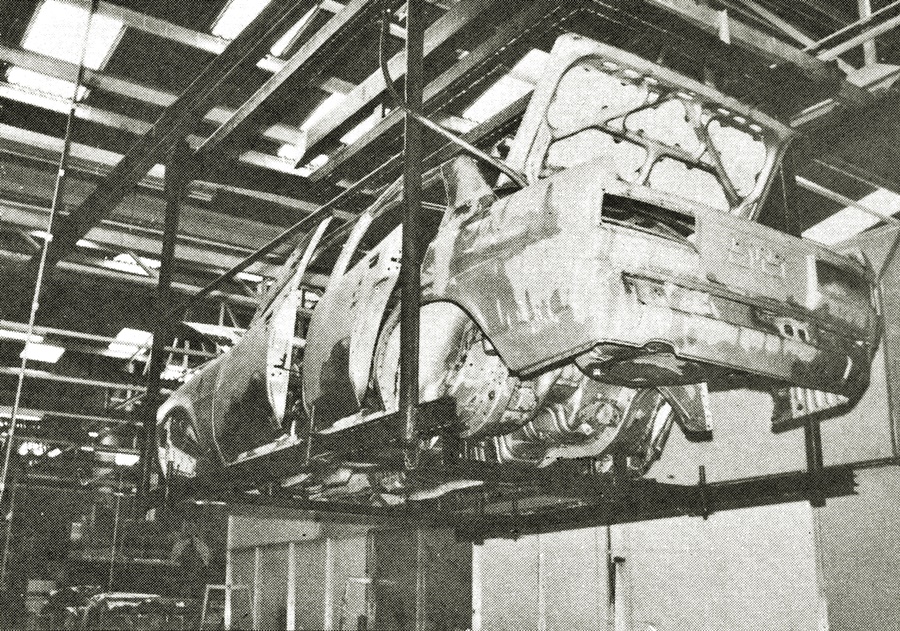
Up till the 1980s, Malaysia was an excellent place for any carmaker to have a production base. It had a good infrastructure, a well educated workforce which was also familiar with the English language, a stable government and a growing economy. It had begun local assembly activities in 1967 so a broad range of locally-made components was available. Manufacturers who chose to assemble locally had their vehicles taxed at lower rates so they could be priced attractively.
However, things changed after the mid-1980s when Malaysia decided to have its own National Car, with the government being an investor in the project. Naturally, it had protection so it could compete against established brands and with the protection, the playing field was no longer level like before. The market came to be dominated by one brand while others had to fight in a far smaller slice of the market.
In the interests of ‘free trade’ and also as a member of the World Trade Organisation, the government never stopped anyone else from selling in Malaysia. They were welcome to import their vehicles in CBU (completely built-up) form and pay much higher taxes, or assemble them locally and have lower taxes but still more than what Proton had to pay.
While having a national car, the government nevertheless wanted to also make Malaysia a production hub in ASEAN. However, it basically wanted carmakers to build their factories in Malaysia but export almost all the production; the domestic market was to be left alone. While this may be fine in theory, as mentioned earlier, manufacturers prefer to look at the domestic market first. If they are to export to another country, why can’t they do it from their own factories in Japan or Europe? The shipping costs would be the same anyway and they would probably have lower production costs as well as the vehicles would be made in high-volume factories with better economies of scale.
The AFTA agreement helped but Malaysia has so far not benefitted much. When the manufacturers first learnt of the single market being formed, and the ability to export around the region without import tax, they were attracted. The market size estimated when AFTA was signed in the early 1990s was about 550 million consumers, with many steadily moving upward economically, and a potential GDP of US$750 billion.
So they looked at making investments and besides incentives, they also looked at domestic market potential. Malaysia was seen as ‘protected’ so it was not seriously considered, not that the government really cared since Proton was selling everything it could make anyway. So Thailand, where the playing field was seen as level, got big chunks of investment as Ford and GM built brand new factories to make their products for the region. Indonesia too saw investments with the aim of expanding existing factories to produce more and export.
Ford did consider Malaysia and had a plan to make the Escape SUV in Malaysia for the region. The plans were confirmed but then Malaysia decided that it did not want to open up as planned under the AFTA agreement because it said that its auto industry had been battered by the Asian financial crisis. It needed some extra years to recover, so the market had to stay closed. A frustrated Ford, realizing that it would not be practical to use Malaysia, tore up its plans and put its money into the Philippines where it had a factory.
Only Volvo seems to have chosen Malaysia as a hub of sorts but that is more a historical thing. Its factory here was the first to open when Malaysia began calling for local assembly and although it had production in Thailand, that was closed down and everything concentrated in this country for the region from 2012.
For the other carmakers, Malaysia was still and attractive market because it was the largest passenger car market in ASEAN. Thailand was a pick-up truck market and in Indonesia, the biggest demand was for MPVs. So in spite of the difficult environment, many carmakers continued to operate in Malaysia, make the necessary investments periodically to upgrade their plants and kept refreshing their model lines.
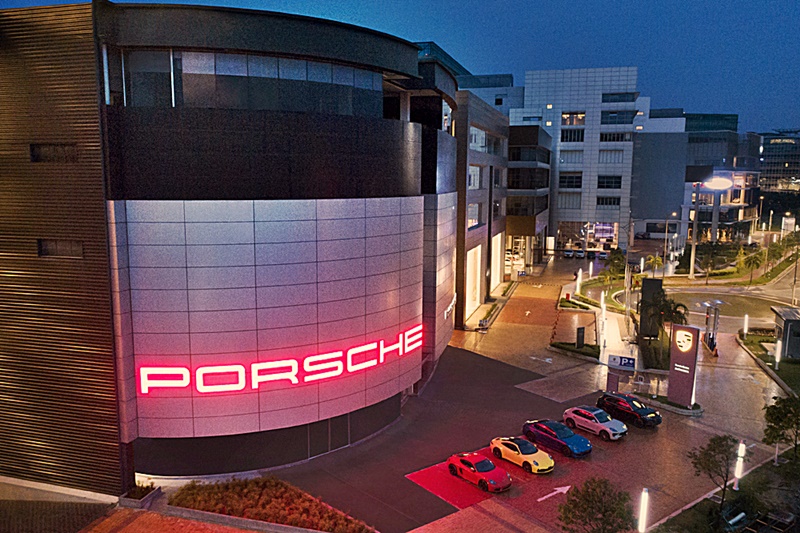
But the much desired objective of the government – to be a regional production hub – remained elusive. There have been a few National Auto Policies (NAP), each one stating that aim, and offering various types of incentives without much detail. The general way that the Malaysian government’s Ministry of International Trade & Industry has liked to operate is with ‘customised’ incentives, perhaps believing that the approach would be more appreciated by investors.
However, many in the industry have expressed a dislike for the approach, preferring the details to be open for all to know and work with. Transparency is important for these businessmen, and as one veteran industry executive said, “How can I know that my competitor might have received a better incentive but actually invested less?”. So the has remained an indifference and even with the latest NAP announced a year ago, the lack of transparency and detail continued. Many people were disappointed that only an outline was provided and could not even begin to start working out plans to propose to their head office. Anyway, since then, the government has changed so it could be that the NAP will see a revised form, depending on the MITI minister.
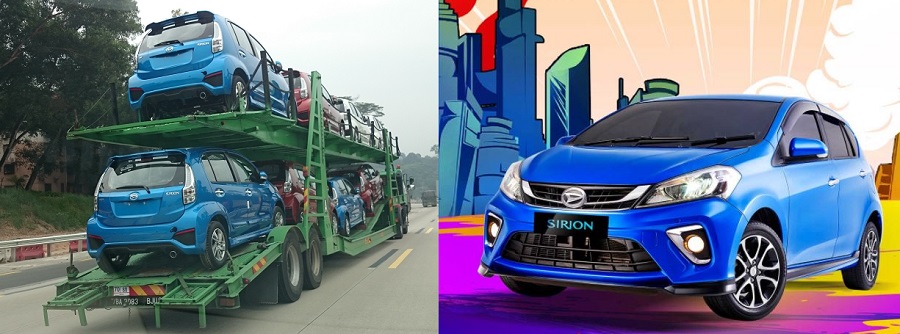
Over the past decade, some companies have tried to export from Malaysia with limited success. Perhaps only Volvo and Mazda (with the CX-5) have been doing well with exports but Toyota started and stopped exporting its Malaysian-made Hiace to Thailand. Proton and Perodua export, of course, and of note is the fact that the Myvi made in Malaysia is taken by Daihatsu for sale in Indonesia as a Sirion under its own brand. That says a lot about Perodua’s quality as a Japanese carmaker would not simply use a product made by someone else.
Porsche and Sime Darby
The report by The Edge Weekly mentions that Porsche will use the Inokom plant in Kedah, which is not surprising. The plant, opened in the late 1990s, is owned by Sime Darby and a unit of the company is also the importer and distributor of the German sportscars. It would make things a lot easier for the same parties to also work together on an assembly project.
If Porsche is indeed going to do it, then it will not just be an assembly program to set up. The carmaker has not done completely knocked-down (CKD) activities before so it will have to set up a new department just for it. Perhaps, being in the Volkswagen Group, it will be able to get assistance from its colleagues in Wolfsburg as there is local assembly of some Volkswagen models being done in Pahang.
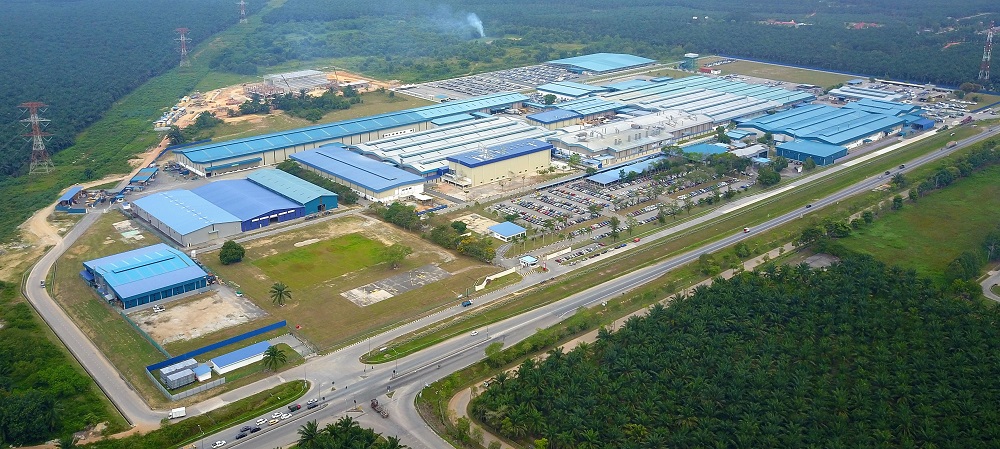
It is not just a matter of picking a model and putting it into a box in disassembled form for assembly in another country. The model has also to be engineered for local assembly, taking into account the level of automation and capabilities of the workforce. This is often the case with picking models for overseas assembly. Volvo had to first invest in laser welding equipment before it could consider assembling the XC60 in Malaysia.
The two Porsche factories in Germany are very advanced with manufacturing processes that ensure high quality. It is unlikely that all the manufacturing processes at Inokom will be identically advanced, so some modification may be needed, and that means an engineering program to develop a ‘Malaysian CKD model’.
It is possible that the ‘SKD’ (semi knocked down) approach will be taken although this approach was stopped by the government in mid-2019. With SKD, bodyshells can be imported already welded together. While the government no longer allows SKD, one never knows with a ‘customized incentive’ and also, the government of today is not the same one that formulated the 2020 NAP.
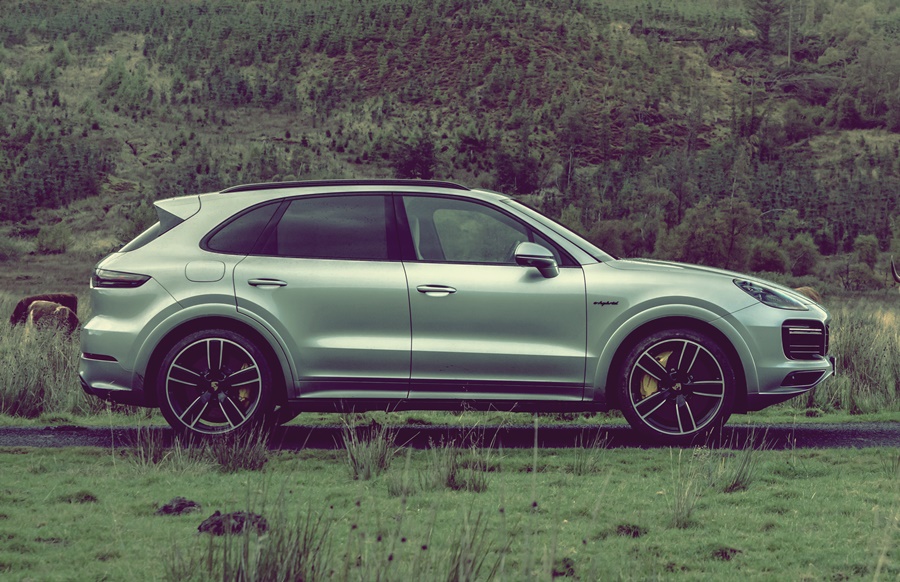
Righthand drive or lefthand drive? This is also another issue, especially if the volume is not going to be very big. What some carmakers have considered – Geely and Great Wall Motors being among them – is that a production hub in ASEAN could be dedicated to righthand drive (RHD) versions which they do not make in their own country. This is more applicable to the Chinese carmakers though as the other global players have long coped with making cars with the steering wheel on either side. So Malaysia could be designated to make RHD models for most of the ASEAN markets and when volumes get higher, then they can also consider LHD.
As for quality, there is nothing inferior about Malaysian assembled vehicles today. The manufacturers have many processes that ensure the quality standards are very high, even if they might not be exactly similar to those of factories in Japan or Germany.
The only thing is consumer perception even though one can say that in this era of globalization, people don’t really care as long as the quality is not poorer. Many years ago, when Proton was assembling the Lotus Elise and tried to export it to Japan, the customers there indicated that if they wanted to buy a Lotus, it had to be made in England. Likewise, when Mazda and Toyota wanted to source some of its models from Thailand for its ASEAN markets, customers in Singapore did not want them and wanted to have cars from the Japanese factories.
Finally, the price – which is often the first thing Malaysians think of when they hear that a model will be assembled locally. For a long time, they have been conditioned to expect that a model that is assembled in Malaysia will be cheaper and that is because there is a lower tax rate and in more recent times, the government also rewards those who make investments with subsidies that can offset production costs to allow lower retail prices. So yes, a locally-assembled Porsche could be cheaper though probably not by a huge amount.