With demand by consumers falling, there is no point in making more cars at this time (apart from the fact that parts may also not be available) so many carmakers are using their manufacturing facilities to produce urgently needed items for the healthcare community.
Toyota is among the carmakers that is helping in many ways and one of the approaches it has taken to indirectly help in the issue of facemask supplies is to make its own. Rather than drawing on the limited supplies in the market and reducing availability to frontliners in hospitals who desperately need them, Toyota is producing facemasks at its Group factories for use by its own workforce.
Although the World Health Organisation (WHO) had earlier stated that facemasks are not necessary for those who are not ill, it has since changed that position. A senior WHO official said that ‘the use of masks, both home-made and cloth masks, at the community level may help with an overall comprehensive response to this disease’.
This change was based on increasing evidence that some people infected with the COVID-19 coronavirus show no symptoms (cough, fever, and in more severe cases, difficulty breathing). As such, they could possibly pass on the virus to others around them. This is why social distancing – standing at least 1 to 2 metres apart – is important if it is necessary to interact. The mask can help reduce the possibility of virus transmission.
Toyota Group factories to make facemasks
DENSO Corporation will self-produce face masks it requires for employees mainly at its production sites. With production of the face masks scheduled to commence during April, they have been working on a prototype. It is anticipated that if things proceed as scheduled, 100,000 face masks will be produced daily.
Toyota Boshoku Corporation’s Kariya Plant, which normally makes textile machinery andcar air-conditioning compressors, is scheduled to commence production of face masks shortly, at a rate of approximately 1,500 face masks per day.
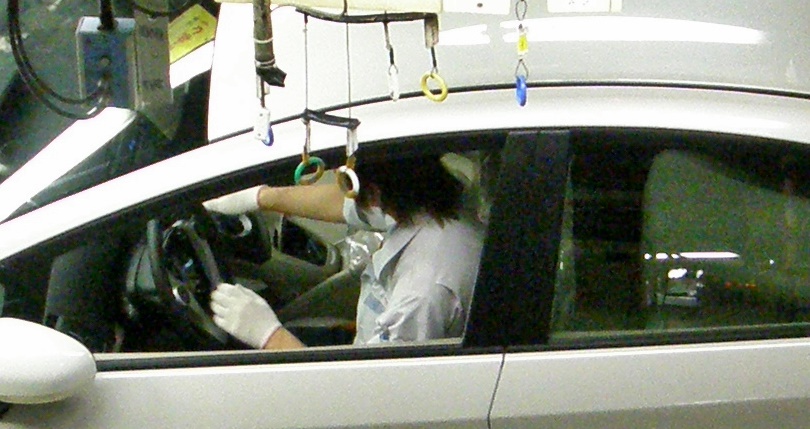
Along with measures to increase production, it is anticipated that production will gradually be transferred to the Sanage Plant from May. The aim is to boost production to eventually reach up to 12,000 face masks per day. In addition, Aisin Seiki, Daihatsu Motor, and Hino Motors are also considering their own production of face masks.
To help with the current shortage of medical face shields, Toyota will produce injection mold and 3D-printed medical face shields. Specifically, a Toyota plant in Japan is preparing to produce injection mold medical face shields with an anticipated starting production volume of 500 to 600 per week. The company is also starting to evaluate the possibility of other group companies also participating in the production.
Using decades-long production expertise
With Toyota’s decades-long experience in mass production, it should be able to develop efficient methods to maximise output of face masks, just as its Toyota Production System has done for making motor vehicles. Some ways that Toyota will help is by considering support measures from various angles by utilizing its global supply chain and utilizing its know-how of manufacturing and logistics in the fight against the coronavirus.
Toyota Mobility Foundation offers connected and sanitized mobility services