Before the 1970s, corrosion in metal car bodies was a problem and one of the reasons was that the protective layer of primer paint was not effectively applied over the metal surfaces. It was manually sprayed on so there would be some little sections that may not have been covered. And like a cut in your skin allowing germs to enter your body and infect you, a small unprotected spot on the metal could allow corrosion to start.
This changed when the electro-deposition (ED) dipping process was introduced where the entire bodyshell was submerged in a giant tank of primer paint. It was covered 100% and even the cavities got properly covered. After the 1970s, corrosion issues reduced significantly. Galvanization of the steel (adding a zinc coating) also made a big contribution to reducing corrosion and enabling vehicles to last longer.
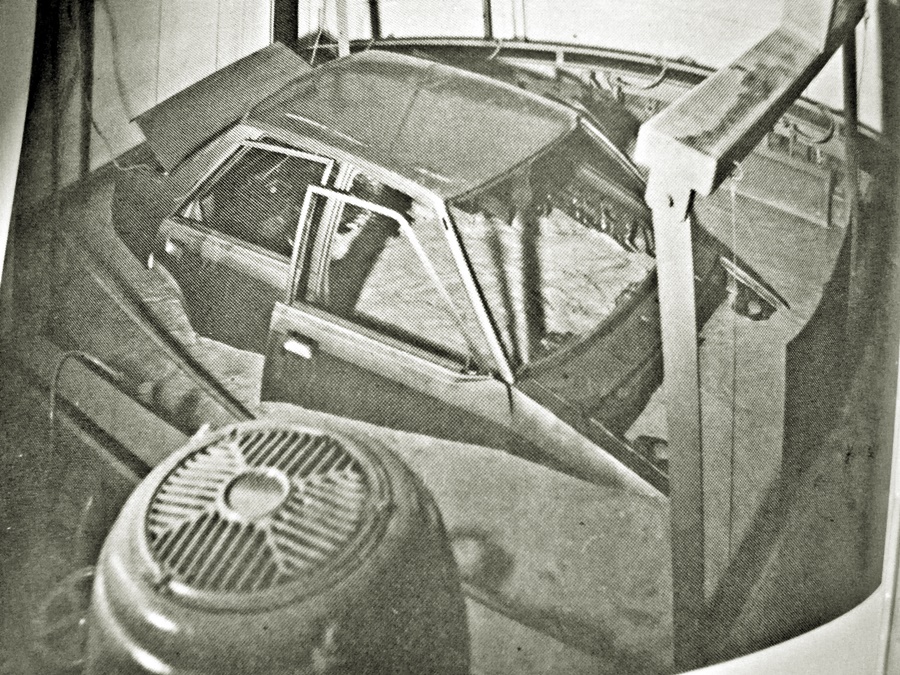
Over the primer goes coloured paint that is sprayed on either manually or in many plants these days, with robotic spraying machines. The quality of application has improved greatly over the years, but coating efficiency has been around 60% to 70%, which you aren’t like to notice but to the quality control people, it is a known issue.
95% coating efficiency
Now Toyota has developed a new type of airless paint atomizer that achieves over 95% coating efficiency (the amount of paint sprayed versus the amount that actually adheres onto the vehicle body), the highest in the world. The machine – the first of its kind in the world – uses static electricity instead of air, to replace the conventional air paint atomizers used in the vehicle body painting process.
By deploying the airless paint atomizer in Toyota Group’s painting process, it is expected that the factories in the Group can reduce CO2 emissions by about 7% as well. In addition, the collection device situated at the bottom of the paint booth (the area where paint is sprayed) can be made more compact. Therefore, painting production lines in the future can be more compact.
Toyota is advancing initiatives to achieve its Plant Zero CO2 Emissions Challenge, one of the targets included in the Toyota Environmental Challenge 2050 announced in 2015. As part of this effort, it developed the airless paint atomizer and deployed it at both Takaoka and Tsutsumi Plants. Gradual deployment at other plants is planned as well as consideration of deployment among other Toyota Group companies and licensing the technology to other companies.
How it works
Conventional air paint atomizer sprayed paint primarily using aerodynamic force, then paint the vehicle body with the atomized particles using an air paint atomizer. For this reason, paint particles are scattered by the air ricocheting off the vehicle body, with up to 40% lost. By comparison, the new airless paint atomizer uses electricity to spray the paint (electrostatic atomization), and the statically charged particles coat in such a way that they gravitate toward the vehicle body (electrostatic painting).
Electrostatic atomization and electrostatic painting technologies greatly reduce the number of atomized particles that scatter, thereby achieving a higher coating efficiency. In a way, it is like the ED process that has been used for applying primer where electrical charges attract the paint to stick onto the metal.
Click here for other news and articles about Toyota.