Use of recycled materials in car parts has gone on for a long time as carmakers have tried to contribute to sustainable manufacturing processes. However, cost has also to be considered and with new technologies, recycling processes have been cost-effective enough to use.
Many disused items are recycled – from old jeans to coffee beans to coffee bean skins – and PET (commonly abbreviated from Polyethylene tErephThalate) bottles are popular for such use. In fact, the fashion industry produces jewelry, clothes and bags from PET bottles.
Audi is also using recycled material for its new fourth generation A3 for the first time as it continues to follow the corporate strategy of sustainability. The A3’s seat upholstery is made from secondary raw materials are being and up to 89% of the textile used comes from recycled PET bottles.
From old to new
In Germany, there are machines which accept PET bottles from the public, for which they get 0.25 euro (around RM1.20) per bottle. The bottles are then compressed for truck transport in order to save space. Once they have arrived at the recycling plant, they are sorted by colour, size and quality. Foreign matter such as the caps are separated.
A mill then crushes the bottles into flakes, which are washed, dried and melted down. Nozzles shape continuous plastic strands out of the mass. Once they have dried, a machine chops them into small pieces. This results in granulate, otherwise known as recyclate, and this undergoes extrusion to create threads. Wound onto coils, these are used in the final stage to manufacture materials.
In Audi’s case, they are transformed into yarn for the seat fabrics. The company says that in terms of look and feel, the quality standards are the same as conventional textile upholstery.
More than 100 PET bottles in a single A3
Up to 45 PET bottles with a capacity of 1.5 litres are used per seating system. On top of this, an additional 62 PET bottles are recycled for the carpet in the new A3. Other components in the interior are also increasingly made of secondary raw materials, eg insulating materials and absorbers, the side panel trims of the luggage compartment, the loading floor and the mats.
At present, the seat upholstery is not yet made completely of recyclable material. “The lower layer of woven material, which is connected to the upper material with adhesive, is what poses the challenge. We are working on replacing this with recyclable polyester,” says Ute Gronheim, who is in charge of material development in the textiles division at Audi. “It is our goal to make the seat upholstery completely from unmixed material so that it can be recycled again. We are no longer very far away from this.”
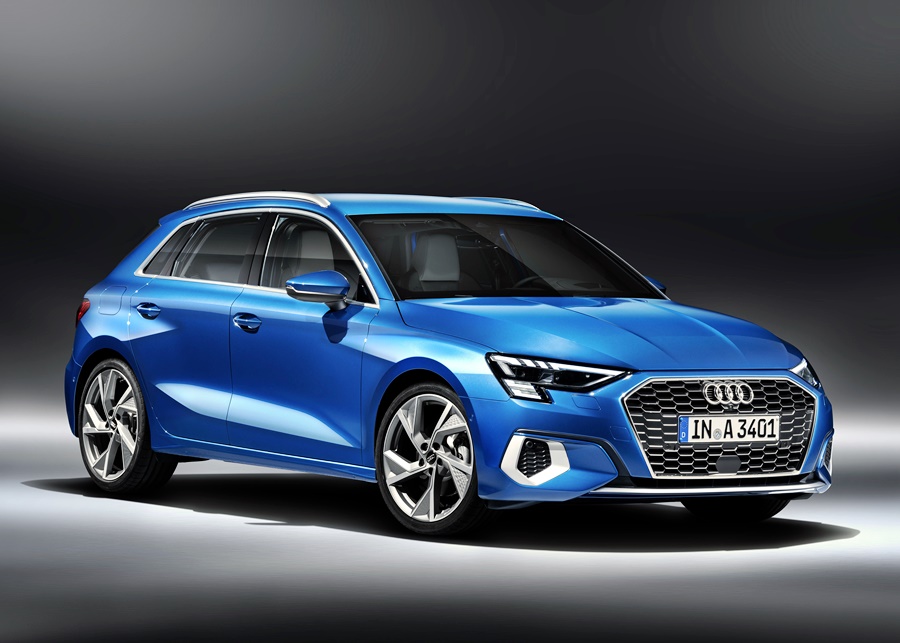
In the long term, all seat upholstery across all model series will be made of recycled material. The goal is clear: the percentage of recycled material in the Audi fleet is to rise considerably in the coming years.