Drinking water is good for you and many take water bottles with them in their car or bag when they go out. However, where the empty bottle ends up is not always certain. Those who care for the environment will make sure they dispose of the plastic bottle in the right place, like a rubbish bin if not a recycling centre. Many though will just throw it by the roadside without a thought and if not collected, it will remain there for the next 450 – 1,000 years, depending on the type of plastic used.
In coastal areas, the bottle may wash into a drain and then into the sea where it joins other rubbish – and more plastic bottles – that float around. Sea creatures are at risk and in areas such as the Pacific gyre, there is a floating mass of plastic bigger than the size of Mexico in the Pacific Ocean!
Carmakers undertake recycling activities
It’s a big challenge getting mankind to stop such pollution so car companies like Ford are helping by using recycled plastic bottles for auto parts. Ford’s use of recycled plastics dates back to the 1990s. In the past decade, aerodynamics has driven the need for underbody shields, and the use of plastics in vehicle parts is used globally and has grown exponentially. Ford uses about 1.2 billion recycled plastic bottles per year – about 300 bottles per vehicle on average.
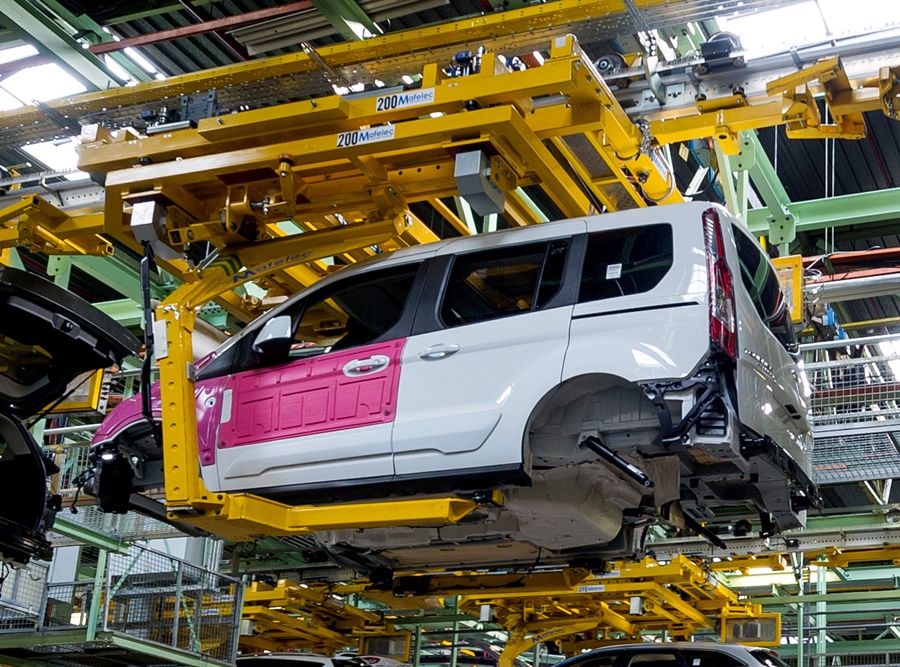
One area where the plastic bottles are used is the underbody shield of the car. “The underbody shield is a large part, and for a part that big, if we use solid plastic it would likely weigh 3 times as much,” said Thomas Sweder, a design engineer at Ford Motor Company. “We look for the best materials to work with to make our parts, and in this case, we are also creating many environmental benefits.”
Ideal material
Due to its light weight, recycled plastic is ideal for the manufacture of underbody shields, engine under shield, and front and rear wheel arch liners that can help improve vehicle aerodynamics, which impacts fuel efficiency.
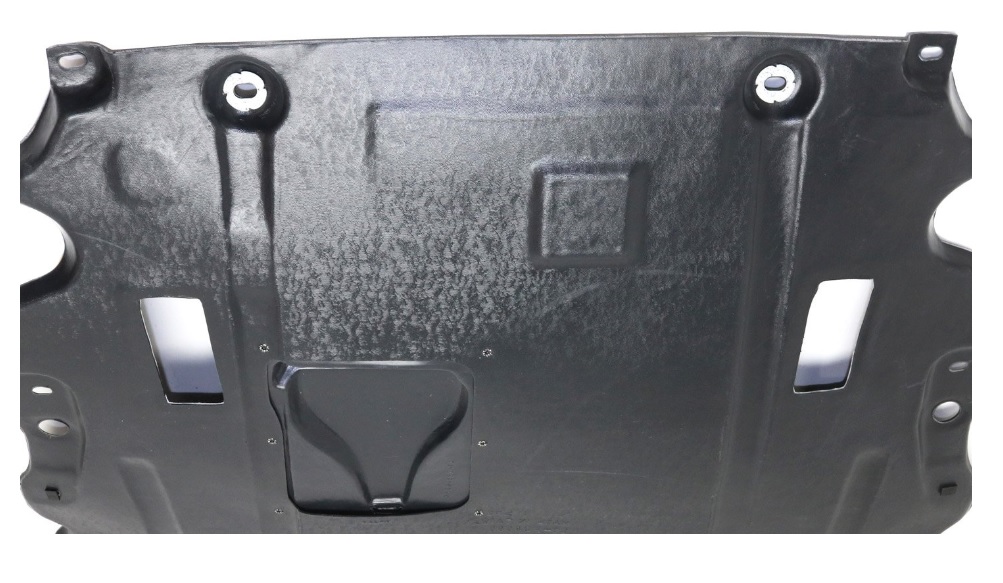
Here’s how it works: when plastic bottles are thrown into a recycling bin, they are collected with thousands of others, and shredded into small pieces. That’s typically sold to suppliers who turn it into a fibre, by melting the bottle and extruding it. Those fibres are mixed together with other various types of fibre in a textile process and used to make a sheet of material – which is then used to make the automotive parts.
“Ford is among the leaders when it comes to using materials such as this, and we do it because it makes sense technically and economically as much as it makes sense for the environment,” Sweder said. “This material is very well suited for the parts we’re making with it and is extremely functional.”
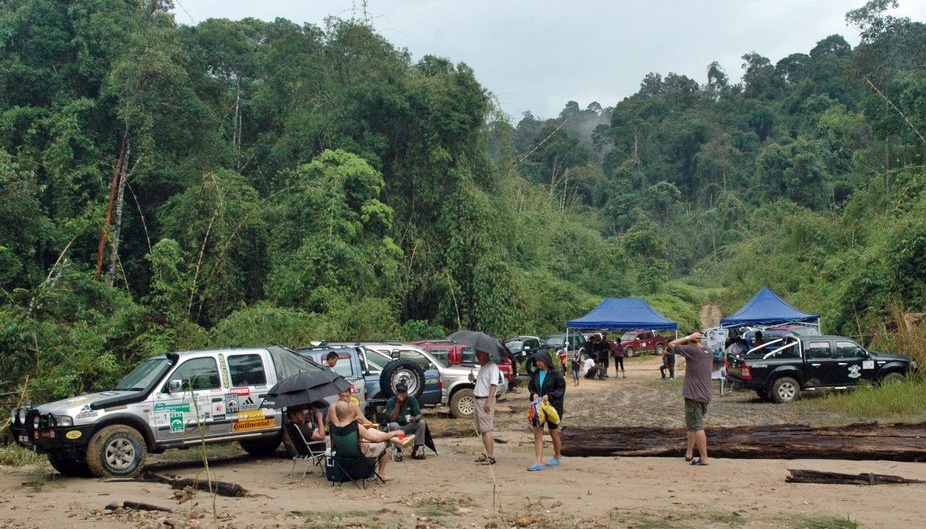